Epok c'est le service informatique externalisé des TPE/PME
Depuis maintenant 17 ans nous installons, développons et maintenons les Réseaux Informatiques et Telecoms de nos clients, qui sont chaque jour de plus en plus nombreux.
Nous faisons avec chacun de nos clients le pari de devenir un véritable service Informatique et Telecoms à part entière afin de leur apporter de la réactivité, de l'innovation et les soulager de tout ce qui touche de prêt ou de loin à la gestion de l'ensemble du système d'information de leur entreprise.
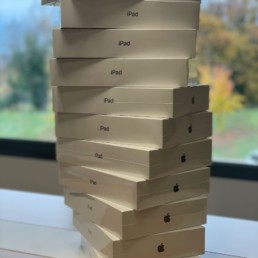

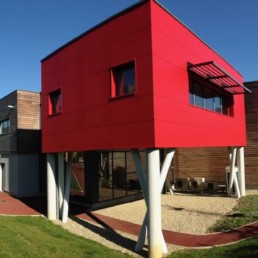
Actualités
Un service de proximité
2006
Depuis 17 ans, notre ADN s’inspire de nos clients. Nous adaptons l’informatique aux entreprises et à leurs spécificités.
1500
Sur site ou à distance, nous supervisons l’ensemble des outils Informatiques de nos clients. Mac ou PC, Serveurs, Smartphones, hébergement web et mail, sauvegardes…
Proximité
Nous sommes là pour nos clients
Ecoute
Nos clients ont des demandes, des besoins, nous savons les écouter.
Réactivité
Nous nous efforçons d'apporter une solution rapidement et efficacement.
Innovation
Parce que le monde bouge, nous bougeons avec lui et proposons des approches nouvelles lorsqu'elles apportent un véritable bénéfice à nos clients.
Les Sites Web
La création d’un site web pour une entreprise est un processus complexe qui nécessite une planification minutieuse, une conception efficace et un développement professionnel. Il est important de prendre le temps de définir les objectifs et les besoins de votre entreprise pour créer un site web qui soit à la fois fonctionnel et attrayant pour les utilisateurs.
À ne pas manquer !
Bénéficiez de nos tarifs négociés sur le neuf et de nos produits sélectionnés et reconditionnés par nos soins